A bright idea?
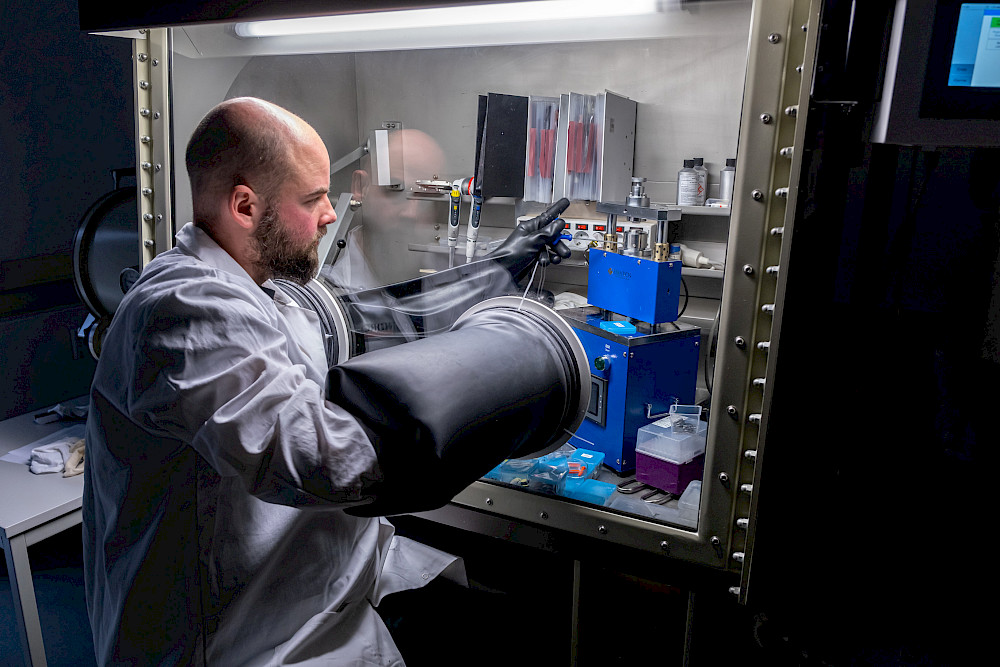
Two and a half years ago, Udo Reichmann and Marcel Neubert – two young physicists from Dresden – knocked on Dr Hartmut Leipner’s door. They were eager to share their idea of replacing the conventional graphite anode in lithium-ion batteries with silicon to make them at least ten times more powerful. “I thought it would be a brief and disappointing conversation, because the idea wasn’t new and had always failed in the past”, Leipner recalls. “But I was wrong, because it has since developed into a promising project”.
The charging capacity of graphite
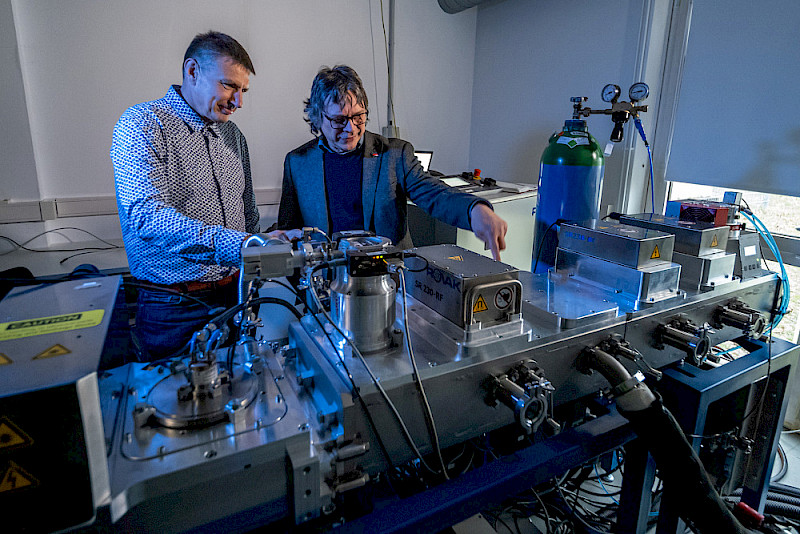
Hartmut Leipner is the Chief science officer of the Interdisciplinary Center of Materials Science (IZM) at the MLU, where a great deal of research is being carried out on semiconductor technologies, solar panels and batteries. The center has a clean room with several ultra-high vacuum facilities for the production of thin-film materials, as well as high-performance scanning electron microscopes and other high-resolution analysis technology. “The young scientists were attracted by our expertise and technical equipment”.
The idea presented by the Saxon physicists is logical. To understand this, here is a brief digression… Lithium-ion batteries essentially have four main components: two electrodes, a highly conductive electrolyte and ions as charge carriers. When the battery is charged, lithium ions move over to the negative electrode (the anode). During the discharging process, the ions move back to the cathode, where electrons are released – the battery supplies electricity. “In most lithium-ion batteries, the anode is made of graphite”, explains Leipner.
“Graphite is very stable and can withstand thousands of charging and discharging processes”. However, the disadvantage is that not so many lithium ions can be stored in the narrow spaces between the layers of carbon, which significantly limits the battery capacity. Silicon, on the other hand, has a regular atomic lattice with large gaps and can absorb around one hundred times more lithium ions than graphite. Theoretically.
Structure deformed by flashes of light
However, experiments have shown that silicon anodes expand greatly when ions are absorbed and contract again when ions are discharged. This repeated change in volume causes them to quickly become brittle and fail. Marcel Neubert from the Helmholtz-Zentrum Dresden-Rossendorf (HZDR) and Udo Reichmann from Rovak GmbH in Grumbach, who met each other while studying physics at TU Dresden, didn’t want to give up on the concept of silicon anodes. They came to Halle with the crazy-sounding idea of destroying the atomic lattice with short flashes of light from a very powerful xenon lamp. They didn’t want to destroy the atomic lattice completely, but only to the extent that the structure would become more stable as a result of the deformation while maintaining enough holes to absorb as many lithium ions as possible. Marcel Neubert: “You can imagine it like this: The model of an atomic lattice, as taught in physics classes, can easily be compressed or expanded. If you briefly expose it to heat and quickly cool it down again, some areas fuse together, forming irregular clumps and stabilising the lattice”.
Hartmut Leipner isn’t the only one who was persuaded by the idea; the project has also been granted 750,000 euros in funding from the European Regional Development Fund (ERDF). Over the past two years, these funds have been used to support two scientists each from the MLU and NORCSI GmbH, a company founded by Reichmann, Neubert and two other colleagues in 2020. The practical laboratory is based at NORCSI in the Weinberg Campus Innovation Hub. This is where the battery prototypes are manufactured and tested. The centrepiece is a semi-automated vacuum system in which several layers of silicon are vapour-deposited on copper foil and then flashed for a few milliseconds. “The rest of the process hardly differs from conventional battery production”, says Neubert. “We punch out the foil and integrate it into a button cell together with a metal oxide cathode and an electrolyte”.
The IZM is mainly responsible for characterising the samples. For example, a scanning electron microscope can be used to see how the silicon structure is affected by modifications to the intensity and duration of the flashes. While prototypes are produced at NORCSI, alternative vapour deposition methods and material combinations are also being researched in the IZM clean room. Hartmut Leipner: “We’re a bit like the testing laboratory at molecular level, but we’re also involved in strategic project development”. The researchers are now hoping to receive follow-up funding for another two years.
3,000 instead of 300 kilometres
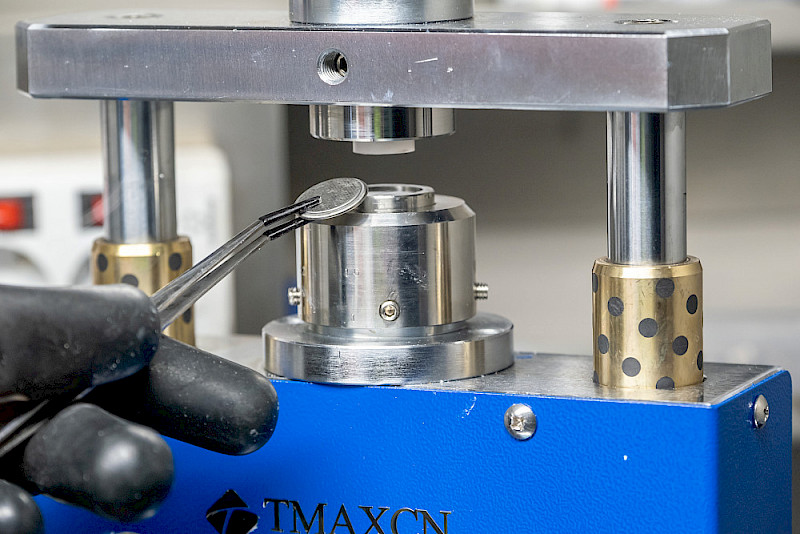
The NORCSI button cells can currently withstand over 100 charging cycles under more stringent laboratory conditions, which corresponds to between 500 and 1,000 cycles in practice. In other words, they can match established lithium-ion batteries in terms of stability. After entering into a partnership with TU Bergakademie Freiberg, the founders are now thinking about manufacturing on a larger scale.
The researchers estimate that only a tenth of the charging capacity of the silicon anode, which is theoretically one hundred times higher than that of graphite, will be achieved in practice. “But to put things into perspective, that means that a car battery would increase its range from 300 to 3,000 kilometres without changing the size of the battery”, says Hartmut Leipner. “That would add fresh impetus to the acceptance and expansion of the e-mobility sector”. At the same time, the new generation of lithium-ion batteries would make it possible to build much lighter devices – not only tablets and laptops, but also drones, for example, where every gram matters.
Dr Hartmut Leipner
Interdisciplinary Center of Materials Science
phone +49 345 55-28473
Mail hartmut.leipner@cmat.uni-halle.de