Design meets science
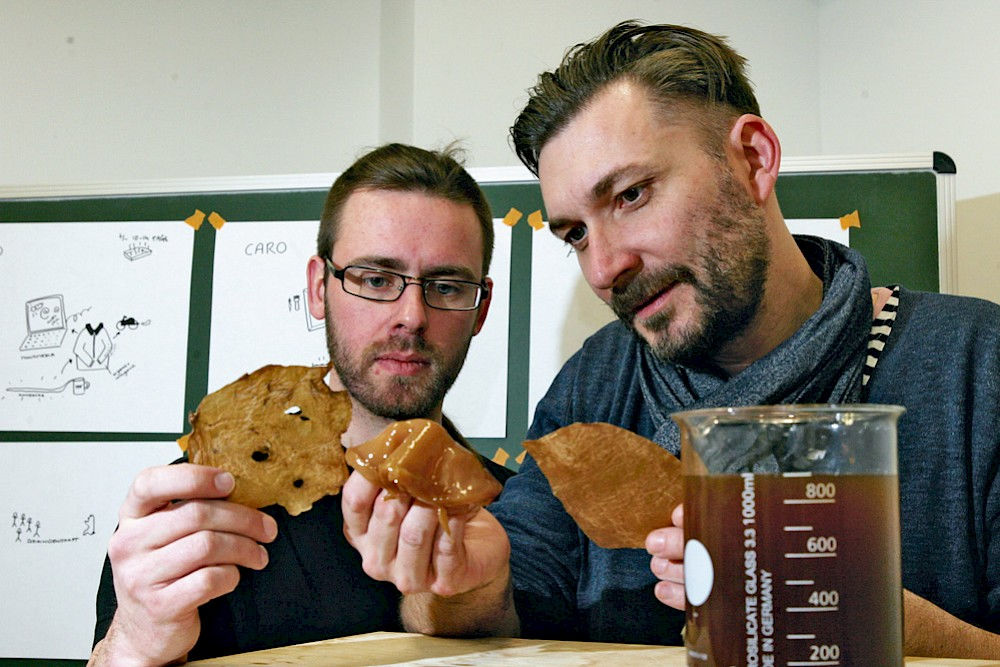
When scientists meet designers, then, according to process engineer Dr. Sandra Petersen, this is ideally what happens: “Working together with students from the Burg University has re-opened our eyes. When we look for applications for processes, we usually direct our attention at products that already exist and try to optimise them. The design students, on the other hand, have pointed us in completely new directions.”
In 2013 she coordinated a joint project between the Chair of Thermal Process Engineering at MLU and the Burg’s Industrial Design programme. The research team surrounding Professor Joachim Ulrich invited Frithjof Meinel, an industrial design professor, and his students to stop by. The engineers explained and demonstrated the pharmaceutical crystallisation technique they developed where powder-like materials are portioned and then coated using a second material. It was developed first and foremost to improve the production of pills.
The Burg students were divided into small teams and given two weeks to conceive new design-oriented applications for the process. “At first we felt overwhelmed,” recalls Veronika Schneider, now in her fourth semester as an industrial design student. It was a very strenuous week. “At the end we had the feeling that nothing much of use had been generated.” However the university scientists were impressed with their wide range of ideas at the final presentation.
There were unconventional ideas that opened up a series of new application possibilities: for example “Quickflick” a bicycle tyre repair kit the size of a pill, or the idea of weaving drop-shaped medical substances into textiles. Regardless of whether in the form of a plaster or a tick collar for pets, “this methods is full of potential because it allows for a broad range of application possibilities,” says project leader Frithjof Meinel.
Whether or not the different concepts will actually be implemented can often only be gauged by the scientists themselves. “Certainly we haven’t completely understood what lies behind the process,” Professor Meinel adds. “But we did understand the essence of the process. Designers are used to trying to understand the unknown. Breaking down things until they are perceivable – that is our core competency.”
In practice “visual people”, as Meinel calls designers, meet engineers or natural scientists to discuss their ideas together. “Design doesn’t have its own jargon but we teach our students follow-up knowledge so that they can work with key terms from engineering or material sciences.” Trying it out is even better than just discussing it. For example: what can a material do and what can it not do?
How can I make it more pliant, thicker or thinner? Up-and-coming chemists were able to test all this with Burg students at the end of February at the first “Grow” workshop entitled “Exploring Future Materials" at the Institute of Chemistry. Aart van Bezooyen, a material and technology transfer professor at the Burg, and MLU chemist Dr. Filipe Natalio started “Grow” at the beginning of 2014.
Their aim was to create a platform where ideas could be exchanged between art and science - with one joint goal: “Aart and I are interested in developing new and sustainable materials. We both intend to increase their impact and use in the future,” Natalio explains. The project is being funded by the German federal government as part of its Teaching Quality Pact. Open discussions, talks and presentations are also planned at both locations in addition to workshops.
Shells, oil and bees wax
The 28 participants took the topic of the workshop “Discovering Materials of the Future” quite literally. In a chemistry lab, crystals and kombucha cultures were grown, shells were filed and dyed, and bees wax was mixed with oil and heated. “When we know the material better and know how it reacts under specific conditions, we can use it in a more directed way,” says Veronika Schneider. Often things that researchers pay little regard to are particularly interesting: waste or “accidents” – by-products that are generated by chance during scientific research.
When something foams up or boils over it could be the impetus for a new material development process. “We are very much interested in these processes in industrial design. We want to exert influence over them as early as possible in order to exploit a process’s full potential. Once the conceptual phase is over, we are unable to change much,” Frithjof Meinel explains.
For example, if you add a little sugar and a culture medium to kombucha and leave it for a few days, a thick layer of cellulose forms. “If you treat the cellulose with leather oil and then iron it in, a leather-like structure emerges that is very tear and water resistant,” explains Bernhard Schipper who has been experimenting on a test culture since January 2014 along with Karl-Ludwig Kunze, Carolin Wendel and Filipe Natalio.
“The goal is to make this material biologically programmable by adding nanoparticles from metal oxides.” The first conductive motorbike jacket that is capable of reproducing the rider’s mood through LEDs has already been developed. That it is also made from a natural, renewable resource is totally in keeping with the intentions of GROW’s founders.